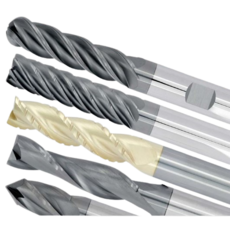
Enhancing End Mill Performance: The Power of Coatings
In the world of machining, precision is paramount. Engineers and machinists are continually seeking ways to optimize tools and processes to achieve higher efficiency, accuracy, and durability. Carbide end mills, the workhorses of machining, play a crucial role in this pursuit. However, even the toughest carbide can benefit from a little extra armor. Enter coatings – the secret weapon that can elevate end mill performance to new heights.
Coatings on carbide end mills serve as a protective shield, enhancing tool life, cutting speed, and surface finish. Among the myriad of options available, four coatings stand out for their remarkable properties: Titanium Aluminum Nitride (TiAlN), Aluminum Chromium Titanium Nitride (AlTiCrN or ALL4), Zirconium Nitride (ZrN), and Diamond-Like Carbon (DLC). Let's delve into the benefits of each and how they can revolutionize your machining operations.
Titanium Aluminum Nitride (TiAlN):
TiAlN coating is renowned for its exceptional hardness, thermal stability, and wear resistance. By forming a tough barrier between the cutting edge and the workpiece, TiAlN-coated end mills exhibit prolonged tool life, reduced friction, and increased chip evacuation. This translates to longer uninterrupted machining cycles and higher productivity. Whether you're tackling steels, stainless steels, or high-temperature alloys, TiAlN-coated end mills prove their mettle in the most demanding applications.
Aluminum Chromium Titanium Nitride (AlTiCrN or ALL4):
ALL4 coating takes the benefits of TiAlN to the next level by incorporating chromium into the mix. The result? An end mill coating with superior oxidation resistance, enhanced hardness, and improved lubricity. ALL4-coated end mills excel in high-speed machining in ferrous applications, delivering impeccable surface finishes and unparalleled performance. Say goodbye to built-up edge and hello to optimized cutting parameters with ALL4 at your disposal. All 4 is standard on all our HEM High Efficiency Milling tools.
Zirconium Nitride (ZrN):
When it comes to machining aluminum & non-ferrous materials, ZrN coating emerges as the coating of choice. Renowned for its low coefficient of friction and chemical inertness, ZrN-coated end mills effortlessly glide through challenging materials, minimizing tool wear and maximizing tool life. Additionally, the gold hue of ZrN coating adds a touch of style to your tool arsenal while serving as a visual indicator of wear, prompting timely tool replacement and preventing costly downtime.
Diamond-Like Carbon (DLC):
For the ultimate in hardness, smoothness, and durability, look no further than DLC coating. Composed of carbon atoms arranged in a diamond-like lattice, DLC-coated end mills exhibit extraordinary resistance to wear, adhesion, and chemical attack. This makes them ideal for machining abrasive composites, hardened steels, and exotic materials with unrivaled precision and reliability. With DLC-coated end mills, you can push the boundaries of machining performance while maintaining impeccable surface integrity and dimensional accuracy.
Conclusion:
In the ever-evolving landscape of machining, the right tools can make all the difference. Coatings on carbide end mills serve as a force multiplier, enhancing performance, extending tool life, and unlocking new possibilities in precision manufacturing. Whether you're seeking exceptional hardness, superior oxidation resistance, or unmatched wear resistance, there's a coating tailored to meet your needs. Embrace the power of coatings and unleash the full potential of your machining operations. Your quest for excellence starts here.
Skookum Carbide End Mills