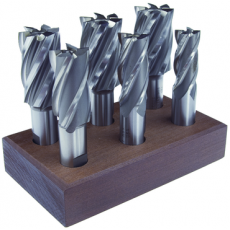
What exactly is an End Mill?
At first glance, you might think that end mills are just different types of drill bits. As the name suggests, however, end mills are used in milling applications and are a type of cutting tool. There are several categories available, and they may be further divided by the application, such as slotting, side milling, tapering, or pocket milling.
What is Milling?
To have a better understanding of end mills and their uses, one needs to know what milling is. In basic terms, milling is a technique that uses a rotating cutting tool to carve out 3-dimensional shapes. As the end mill rotates, it removes material from the piece being worked, and its shape determines the result.
Milling is done by inserting the chosen end mill into a milling tool holder that in turn is placed within the tool spindle on the machine.
Types of End Mills
Square end mills are used for most general applications, but as mentioned above, end mills come in a variety of shapes useful for achieving different effects. Centre-cutting end mills have cutting surfaces on both the sides and the face, which makes them the right choice for plunge-milling. Non-centre end mills only have cutting edges along their sides, and they are easily identified by a small hole in the centre and are used for side milling.
When needing to remove large amounts of material quickly and without vibration, roughing end mills are your choice. These are useful for speed but lack finesse. Roughing end mills have serrations that produce numerous small chips and rough edges (hence the name). There are roughing and finishing end mills, however, which not only remove heavy material, but also leave a smoother finish.
Ball end mills are another useful type of end mill and will produce a radius at the bottom of slots and pockets. They are put to good use when you need to do some contour milling, shallow slotting, or pocketing.
These are just some of the different types of end mill, with several other types available to suit every application.
What Are Flutes?
Flutes are the spiral-shaped cutting edges along the side of the end mill. During use, the material being cut away can move along these channels if the end mill is in a pocket or slot. Typically, there will be 2- 4 flutes.
When an end mill has more flutes, it has more cutting edges, but that results in smaller channels for material to move along. For that reason, you need to be aware of the “chip load,” which indicates the thickness of the material being removed by each of the cutting edges. The number of flutes should match the material being cut and the machine you are using.
• Two flutes provide the most flute space, good for softer materials and non-ferrous materials like aluminum.
• Three flutes give a better finish to hard materials. Three flutes give the end mill greater strength but may cause issues with chip removal.
• Four flutes are well-suited to finish milling, but as with three flutes, chip removal may be an issue.
Materials and Finishes
End mills may be made from a variety of materials, such as high-speed steel (HSS), cobalt, or solid carbide, and feature finishes such as Titanium Nitride (TiN) and Aluminum Titanium Nitride (AlTiN) that will affect wear resistance, cutting ability, and the ability to run at higher speeds.
End mills are cutting tools used in milling operations, which involve the machining of a workpiece with a rotating cutter. These tools are commonly used in milling machines, CNC machines, and other machining equipment. End mills feature cutting edges on the bottom and sides and come in various shapes and sizes to perform specific tasks. Some common uses of end mills include:
-
Milling: End mills are primarily used for milling operations, which involve removing material from a workpiece to create a desired shape, profile, or feature. They can cut in various directions (up, down, or sideways) depending on the type of milling operation.
-
Profile Cutting: End mills are used to cut profiles or contours into a workpiece. They can create complex shapes, slots, pockets, and other intricate features with precision.
-
Slotting: End mills are commonly used to cut slots or grooves into a workpiece. They can create narrow or wide slots of varying depths and widths.
-
Drilling: End mills with center-cutting capabilities can be used for drilling operations, allowing for both drilling and milling in a single operation. This is especially useful for creating holes with precise dimensions.
-
Facing: End mills can be used for facing operations, where the cutter removes material from the surface of a workpiece to create a flat and smooth finish. This is often done at the beginning of a milling operation to ensure proper alignment and surface preparation.
-
Ramping and Helical Interpolation: End mills are utilized for ramping and helical interpolation operations, which involve creating inclined or helical paths in the workpiece. This technique is commonly used in aerospace, automotive, and mold making industries.
-
Contouring and 3D Machining: End mills are essential for contouring and 3D machining applications, where intricate three-dimensional shapes and surfaces need to be produced with precision.
Overall, end mills are versatile cutting tools used in a wide range of manufacturing and machining processes across various industries, including automotive, aerospace, electronics, mold making, and general machining. Their ability to create precise features and complex shapes makes them indispensable in modern machining operations.
With such a variety of end mills available, you will be able to tackle any application. The experts at Skookum Tools are here to help find the right one for you, to ensure that all your projects go smoothly. Please take a look at our Skookum Brand End Mills HERE