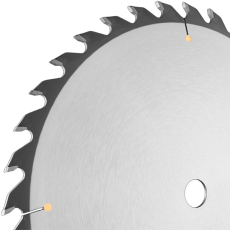
Choosing the best carbide tipped saw blade
It can be quite a daunting task, but once you break it down and understand what each difference makes, you can select a great blade for your specific cutting job.
-
Determine the correct diameter of saw blade needed.
This will usually be listed somewhere on your saw and could be indicated in SAE (inches) or Metric (millimeters). So a 10” saw may be listed as 250mm and these are in most cases interchangeable. The outside diameter of a saw does not in most cases need to match exactly but should not be over the specified diameter for the tool. So a 7-1/4” Circular saw can normally do just fine with a 7” diameter saw blade but not a 7-1/2” diameter blade.
-
Determine the correct arbour hole diameter.
This can be a little trickier as the diameter of the arbour hole must be an exact match to the saw arbour in order to get a safe and vibration free mounting of the saw blade. If you are not certain of the arbour size, you will need to “guage” it with something that can be quite accurate. Using a mechanical or electronic caliper is a great way to check but if you do not have one of those you can use a tape measure or ruler, just make sure you are measuring the full outside edges so you don’t get tricked between some very close size arbours like 1” and 25mm. Fortunately, there are not a lot of saws that require a 25mm bore so your size will likely be one of the following common arbour sizes; 1/2”, 5/8”, 3/4”, 7/8”, 1”, 20mm, 30mm, 32mm. There are also a number of “special” arbours like; diamond shaped (usually for portable saws) and metric with pinholes or keyways. Make sure you get an exact match on these!
-
Understanding tooth styles and their usage.
ATB = Alternating Top Bevel with a positive rake – This tooth pattern has an alternating sloped top grind that can come in varying degrees of angle. The 15 degree is typical for general purpose crosscutting of wood and plywood. The positive rake indicates that the tooth “leans forward” which helps the blade bite into the material without a large amount of feed pressure.
Hi-ATB = High Angle Alternating Top Bevel – These come in a 30 to 40 degree top bevel with a negative rake. This version is especially suited to extra clean top and bottom cutting in fussy materials such as melamine or thin veneered plywood. This blade is also very effective in mitre or chop saw applications for clean mitre cutting of wood mouldings.
TCG = Triple Chip Grind – This is the pattern that looks like the rooftop of a barn when you look at it face on. This tooth has a “ploughing” action that is especially effective when cutting man-made materials like particle board, melamine (best used along with a scoring blade) and when coupled with a negative rake even plastics, solid surface and aluminum.
FTG = Flat Top Grind – Just like it sounds, the teeth on these saws are square top. The most common place you will see these teeth is for ripping (with the grain) solid wood. Usually, with a fairly aggressive positive rake and lots of space between each tooth, these blades will chew through solid lumber quickly. Along with that fast cutting action, you also get a fairly rough cut so be prepared to deal with that after sizing your lumber.
COM = Combination – The utilitarian of wood cutting blades, this blade combines the ATB and FTG patterns into one saw blade. The pattern typically consists of 4 ATB teeth followed by 1 FTG and then a large gap before the next set of teeth. If you are looking for one blade to do a descent job of all of your wood cutting needs then this is your “go-to” blade.
HFG = Hollow Face Grind – This specialty tooth is specifically for cutting Melamine type materials in panel saws. Over the years these blades have dropped in popularity as they are difficult and expensive to sharpen correctly.
-
Choosing the right number of teeth for your blade
In general terms, the more teeth you have on a saw the cleaner the cut will be. There are other factors to consider though when picking the number of teeth. You need to have enough space between each tooth for the saw to be able to carry the chip it just cut through the thickness of the wood you are cutting. The general rule for this to work well for you is not to have more than 2 to 4 teeth in the cut at one time. If you have more than that you will need to reduce your feed rate to give the teeth a chance to clear before making their next cut. The more teeth you have in a cut, the more power you will need in the saw driving it. So, if you have a lighter duty saw with not a lot of extra “oomph” pick a blade with fewer teeth.
-
Should you choose a thin kerf blade or regular kerf?
Thin kerf blades are more about needing less power to drive them than saving turning your expensive lumber into too much sawdust (although that still is a consideration!). So if you are looking for a super clean cut without requiring a lot of power, you can go with more teeth in a thin kerf saw. The one major drawback of the thin kerf saw is that they often do not have much steel body to dissipate the heat generated by cutting, so be careful that you don’t overheat the blade by pushing these blades too hard.
So, now that you are armed with the basic information on saw blade selection, think first about what you want this new blade to do for you in the future, along with what equipment you have available, and make an informed decision. As always, we are here to help anytime you need it!
To select your blade, visit our Circular Saw Blade Selector Page HERE